Suzie Edwards Sculpture
2024
Last August I moved my studio from the complex in Kilburn into my home. It was a big step - I miss the artist community in Kilburn but I can now spend more time popping into my home studio. I treated myself to a few bags of clay and just had fun playing...playing with the concept of pear shaped women. I wanted to create strong and grounded but calm female figures. I've had the first few fired at a pottery supplier outside Reading and the next batch are nearly ready to go. I've been using black clay (it's beetroot colour raw and very messy!) and love the results. Here are some photos from the studio.




March 2023
I put together a video about the Lost Wax Bronze Casting Process for the exhibition and thought it might be interesting for visitors to my website:

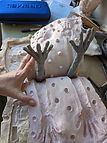





It's been a very busy few months in the studio creating new work, having moulds made, liaising with the foundry, casting, colouring, mounting.....and organising an exhibition! Here are some photos of works in progress

Playing around with clear resin trying to make water splashes for a sculpture. This is all experimentation but still fun!
Quite often disasters in the studio produce something workable - in this case a pair of plaster feet I might colour and keep for myself.

Lost wax process
All my bronzes are cast using the Lost Wax Method - people don't realise that this ancient method of bronze casting involves many stages so I'm going to try to document the process below. I hope you find it interesting.

A mould is made of the original sculpture so that the piece can be cast multiple times (an edition). This mould is used by the foundry to cast a copy of the sculpture in wax. The wax is checked by the sculptor at this point and worked on if necessary. This is also when it can be signed and the edition number added.

I'm wearing magnifying glasses to inspect my piece.
The experts at the foundry then add wax sprues, runners and risers to the wax "sculpture" to strengthen it and allow the molten bronze to flow easily when that stage is reached.
A ceramic shell is then built up over the wax in layers until the shell is thick and strong enough.
Next the shell is heated to melt out the wax and leave a (sculpture shaped) void ready for molten bronze.
The shell is then fired in a kiln in preparation for the bronze pour.

Bronze is melted to around 1100 degrees and poured into the ceramic shells.

This is one of my sculptures, freshly cast, having been smashed out of its ceramic shell.
The metal workers at the foundry remove any metal sprues, runners, risers and clean up the sculpture. Large sculptures may have been cast in pieces and the skilled metalworkers put it together in such a way that the seams will not be visible. The sculptor then comes to the foundry for a metal check and once he/she has approved, the piece goes to be patinated which is where colour is added by using heat and chemicals.

This is one of my pieces being expertly patinated by Matt at BronzeAge foundry in East London. This is my favourite part of the process as the piece starts to come to life. Cast bronze is surprisingly dull and patination is an art form in itself. Each piece is patinated separately and is therefore unique.
Many thanks to BronzeAge Foundry (London) and Taurus Bronze (Suffolk) who allowed me to take these photos.